The final task in the module was to present our work to staff from the Langdon Museum of Power. After a group meeting, we decided to divide our presentation into sections and each group member would be able to talk about the subject they were most comfortable with. We then met again before the final presentation to rehearse.
My task was to discuss the environment and the functions of the various items. Another important point was to emphasise the accuracy of our environment- it was based on plans of the actual brickhouse, whereas other groups may not have reproduced this. Although our environment was not completely accurate- the surroundings would not have been hills, for instance- it was still close.
When presenting, we showed in the background a shot of the model rotating without textures as well as various images of the engine in its environment.
I felt the presentation went well as we all presented our parts of the talk without problems. It was also useful to gain feedback on what we had created - the music in the background would have to be removed if the video was to be displayed in the museum.
Thursday, 3 December 2009
Tuesday, 24 November 2009
Group Work- Making Movies and Finished Product
When it came to creating a movie out of the environment and model, the task of animating the camera movement was given to Kevin. Teresa prepared a voiceover, which I had to cut down as it was quite long, but made sure I left in the most informative parts. I edited the sound in Sony Vegas alongside Kevin's render to create the finished piece.
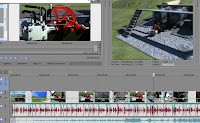
To make the animation long enough to fit the edited voiceover, the animation had to be slowed down to between 50% and 75% speed. I also rendered three additional shots as "filler"- a pan along the tar tanks and above them, as well as a pan along the side of the tunnel. Kevin also contributed an additional closeup shot after a meeting which decided it was required. When choosing a soundtrack, I chose "Robot City" from the film "Robots" as it has a mechanical, industrial feel. The Welsh National Anthem, Land of My Fathers, was suggested as music but when placed with the video it looked quite comical. Teresa also provided sound effects from various coalmines and factories to be used as ambience. Overall, I feel the video is informative as the voiceover explains what the machine is, what it is for and the problems with it.
There is one fault I have noticed in the final model of the machine - the actual machine has a silver ring around the edge of the wheel, which ours had originally. However, at some point between animating the model and merging it with the environment, the wheel and edge sections merged so the red texture now covers both the edge and the main wheel.
Below is the finished video:
Overall I feel we have created a model and animation of good quality, and I believe my environment and textures are up to standard. Although some of my modelling is quite simple, I believe my textures contribute to creating a realistic look to the models.
We have worked well as a group and managed to delegate tasks, and stick to deadlines for getting our parts done. The class sessions have been invaluable for putting our work together and sharing what we have done. There were, thankfully, no major arguments or issues - things largely went to plan and any alterations to the plan were done quickly and easily.
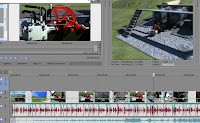
To make the animation long enough to fit the edited voiceover, the animation had to be slowed down to between 50% and 75% speed. I also rendered three additional shots as "filler"- a pan along the tar tanks and above them, as well as a pan along the side of the tunnel. Kevin also contributed an additional closeup shot after a meeting which decided it was required. When choosing a soundtrack, I chose "Robot City" from the film "Robots" as it has a mechanical, industrial feel. The Welsh National Anthem, Land of My Fathers, was suggested as music but when placed with the video it looked quite comical. Teresa also provided sound effects from various coalmines and factories to be used as ambience. Overall, I feel the video is informative as the voiceover explains what the machine is, what it is for and the problems with it.
There is one fault I have noticed in the final model of the machine - the actual machine has a silver ring around the edge of the wheel, which ours had originally. However, at some point between animating the model and merging it with the environment, the wheel and edge sections merged so the red texture now covers both the edge and the main wheel.
Below is the finished video:
Overall I feel we have created a model and animation of good quality, and I believe my environment and textures are up to standard. Although some of my modelling is quite simple, I believe my textures contribute to creating a realistic look to the models.
We have worked well as a group and managed to delegate tasks, and stick to deadlines for getting our parts done. The class sessions have been invaluable for putting our work together and sharing what we have done. There were, thankfully, no major arguments or issues - things largely went to plan and any alterations to the plan were done quickly and easily.
Group Work- Environment
With the model built; textured and animated, the next step was to place it in the environment.
The environment was based on the Bedwas Coal Works in Monmouthshire, where the machine was housed in an outdoor "brickhouse", connected to tar tanks so it could pump the tar up a delivery pipe and into a vehicle. The first stage of building the environment was to obtain some designs, which Teresa had obtained from a former member of staff at the coalworks:
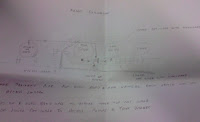
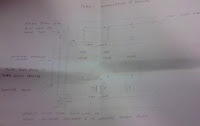
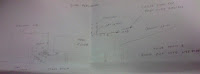
I then began building the environment in 3DS Max, starting with the basic plane floor and cube walls, which I textured using the brick and stone textures and bump maps from my original "factory" environment. The textures had to be tiled differently for each object they were applied to due to the different aspect ratios of the surfaces.
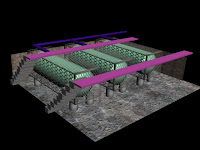
Using cylinders, I could create the masses of pipework which run above the tanks, as well as the supports for the tanks. The tanks themselves are "oil tank" primitives contained within cubes to simulate the cages.
To create the mesh texture for the cages, I made a metal texture in Photoshop and an opacity and bump map to go with it:
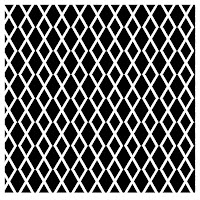
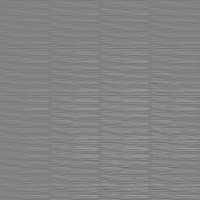
The next step was to texture the tanks, add some more pipework and texture it:
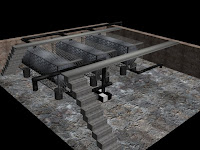
I felt the tanks should have a toughened, steel look to them so I created the following texture and bump map:
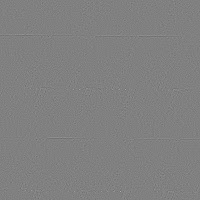
This was created from the following photo I had taken:
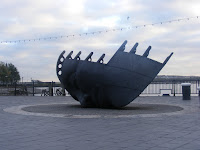
The pipework uses the same texture which was used for the pipes on the model. With the brickhouse complete, I felt it needed some scenery so I created some hills:
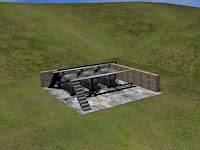
The hills were created by creating a single plane then using soft selection to mould it into a hill shape:
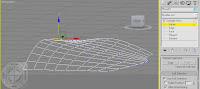
I then cloned this plane to surround the environment and created a flat plane below the stone area to act as ground:
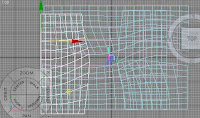
To make the grass texture, I used another photo I had taken and also created a bump map:
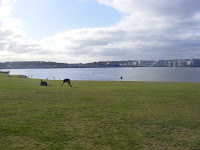
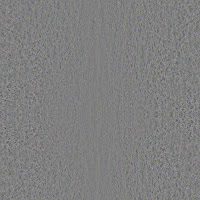
With the main landscape complete, I added a sphere mapped with a double sided material to act as a skybox. The texture used for this was found on the internet:
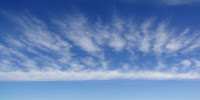
Finally, I added some extra details such as a tunnel, rail track and a small house:
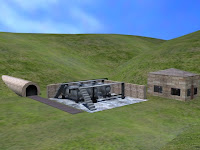
The tunnel is a cylinder which clips into the hillside. The texture and bump map applied to the cylinder is the same as that on the brick walls. In front of the cylinder is a plane with the following original texture and opacity map applied:
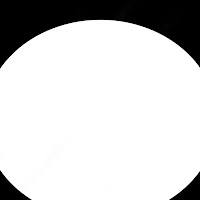
The building is a cube with a pyramid on top, to which I applied the UVW Unwrap modifier so that I could use a UVW Map template to ensure textures all sides of the building were upright:
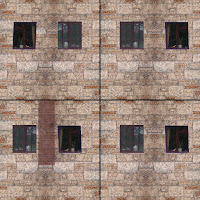
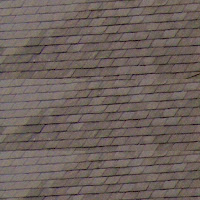
Above is the roof texture. The roof texture and windows on the house were both adapted from this photo I took:
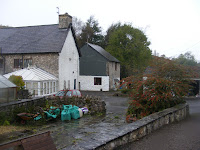
The rail track has the following texture and bump map I have created:
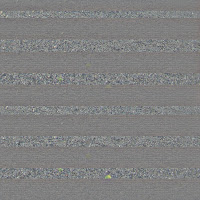
The underlying gravel texture:
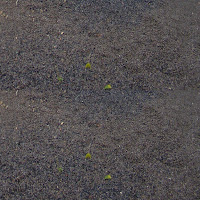
Came from this photo I took:
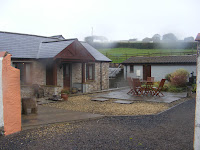
The last stage of the environment was lighting. A single Omni light with ray traced shadows placed high above the scene sufficed. With the environment complete, the final 3D stages were putting the model in the environment and animating the camera movements.
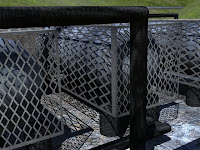
The environment was exported as a 3DS file and imported into the steam engine's Max file to preserve the animation applied to the engine. Once placed in the Max file, the textures had to be reapplied to the environment and the environment itself was scaled to create a realistic image. The final scene was hugely demanding on computing power, with 100 frames taking 2 hours to render in Mental Ray and the final 40 second render took 13 hours.
The environment was based on the Bedwas Coal Works in Monmouthshire, where the machine was housed in an outdoor "brickhouse", connected to tar tanks so it could pump the tar up a delivery pipe and into a vehicle. The first stage of building the environment was to obtain some designs, which Teresa had obtained from a former member of staff at the coalworks:
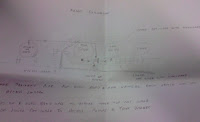
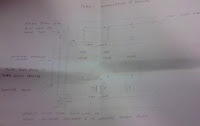
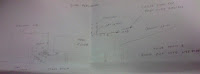
I then began building the environment in 3DS Max, starting with the basic plane floor and cube walls, which I textured using the brick and stone textures and bump maps from my original "factory" environment. The textures had to be tiled differently for each object they were applied to due to the different aspect ratios of the surfaces.
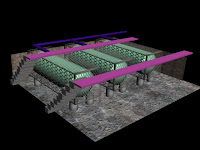
Using cylinders, I could create the masses of pipework which run above the tanks, as well as the supports for the tanks. The tanks themselves are "oil tank" primitives contained within cubes to simulate the cages.
To create the mesh texture for the cages, I made a metal texture in Photoshop and an opacity and bump map to go with it:
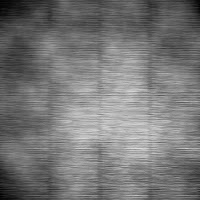
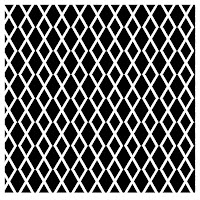
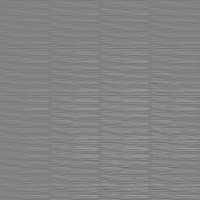
The next step was to texture the tanks, add some more pipework and texture it:
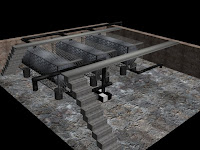
I felt the tanks should have a toughened, steel look to them so I created the following texture and bump map:
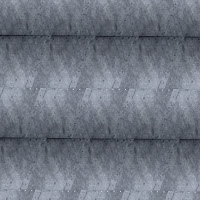
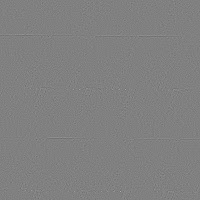
This was created from the following photo I had taken:
The pipework uses the same texture which was used for the pipes on the model. With the brickhouse complete, I felt it needed some scenery so I created some hills:
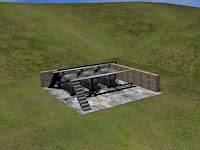
The hills were created by creating a single plane then using soft selection to mould it into a hill shape:
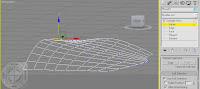
I then cloned this plane to surround the environment and created a flat plane below the stone area to act as ground:
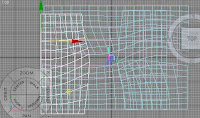
To make the grass texture, I used another photo I had taken and also created a bump map:
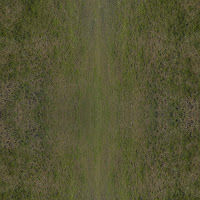
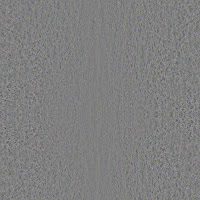
With the main landscape complete, I added a sphere mapped with a double sided material to act as a skybox. The texture used for this was found on the internet:
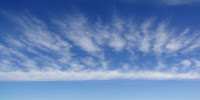
Finally, I added some extra details such as a tunnel, rail track and a small house:
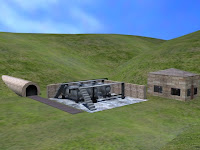
The tunnel is a cylinder which clips into the hillside. The texture and bump map applied to the cylinder is the same as that on the brick walls. In front of the cylinder is a plane with the following original texture and opacity map applied:
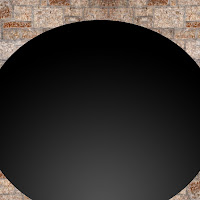
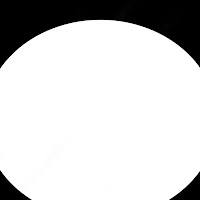
The building is a cube with a pyramid on top, to which I applied the UVW Unwrap modifier so that I could use a UVW Map template to ensure textures all sides of the building were upright:
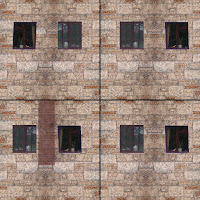
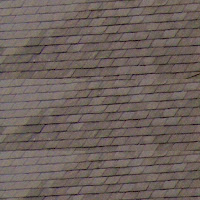
Above is the roof texture. The roof texture and windows on the house were both adapted from this photo I took:
The rail track has the following texture and bump map I have created:
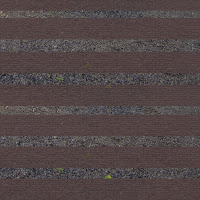
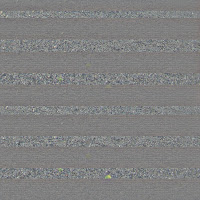
The underlying gravel texture:
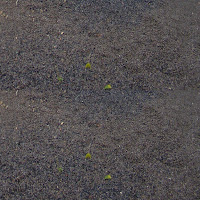
Came from this photo I took:
The last stage of the environment was lighting. A single Omni light with ray traced shadows placed high above the scene sufficed. With the environment complete, the final 3D stages were putting the model in the environment and animating the camera movements.
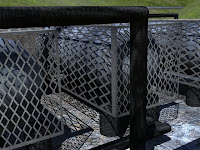
The environment was exported as a 3DS file and imported into the steam engine's Max file to preserve the animation applied to the engine. Once placed in the Max file, the textures had to be reapplied to the environment and the environment itself was scaled to create a realistic image. The final scene was hugely demanding on computing power, with 100 frames taking 2 hours to render in Mental Ray and the final 40 second render took 13 hours.
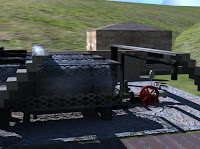
Group Work- Model Textures
The next step of the animation was to apply textures to the model. I created the following in Photoshop and applied the bump map from the stone floor texture to some of them in order to give the images some "texture":
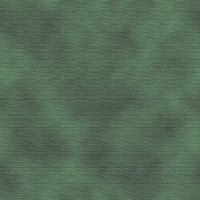
Above - The green texture for the governor housing.
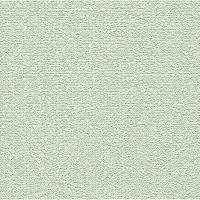
Above - The exhaust housing texture.
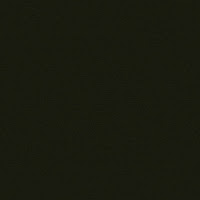
Above- The chassis texture.
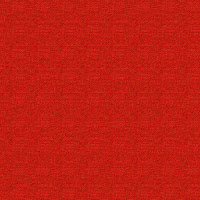
Above- The red wheel and component texture. There are two shades of this to differentiate between red components which sit next to each other.
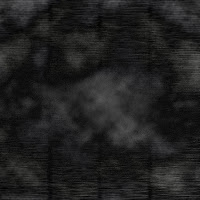
Above- The texture used for pipework in both the model and the environment.
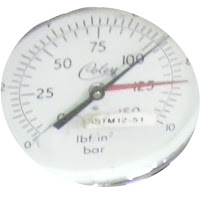
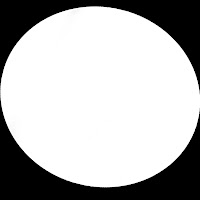
Above is the gauge image, taken from a photo I took at the museum next to its opacity map so the white edges are not visible on the model. It is not a very detailed or precise texture but it serves its purpose in the animation.
Below are images of the model with textures applied:
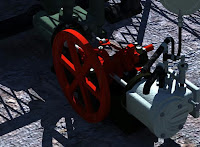
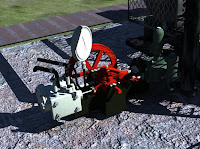
The next step was to place the model in the environment I had created. All aspects of creating the environment will be covered in the next section.
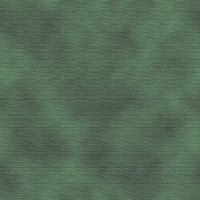
Above - The green texture for the governor housing.
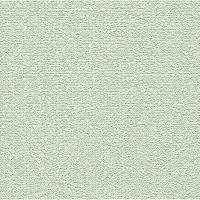
Above - The exhaust housing texture.
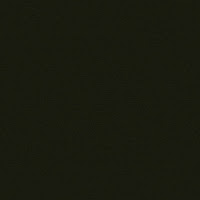
Above- The chassis texture.
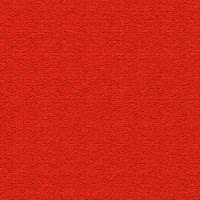
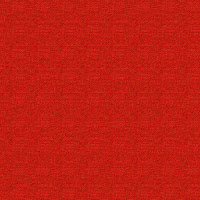
Above- The red wheel and component texture. There are two shades of this to differentiate between red components which sit next to each other.
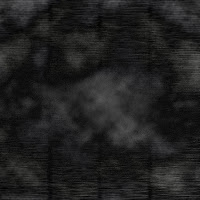
Above- The texture used for pipework in both the model and the environment.
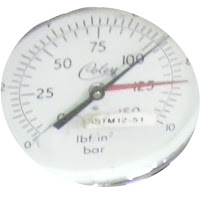
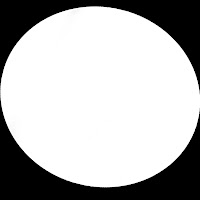
Above is the gauge image, taken from a photo I took at the museum next to its opacity map so the white edges are not visible on the model. It is not a very detailed or precise texture but it serves its purpose in the animation.
Below are images of the model with textures applied:
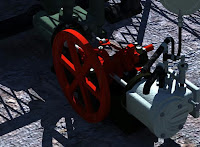
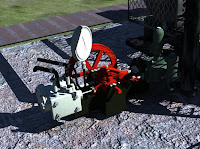
The next step was to place the model in the environment I had created. All aspects of creating the environment will be covered in the next section.
Group Work- Animation and More Alterations
Once Dan had completed the exhaust section, our model was complete. A further alteration to my chassis was made - the loop at the top was replaced by a new segment created by Dan as my loop did not fit the side sections exactly. Below is an image by Dan of the finished model showing everybody's contributions:
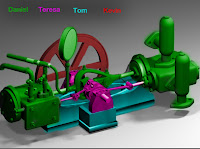
Upon receiving the first video of the animation loop from Kevin...
...It was good to see most of the animation in place. However, certain changes needed to made, which I did in class. The changes I made are:
- On the pump section in the centre, there are floating objects moving alongside Dan's main pump. These should be attached to the pole and not moving, so I removed the keyframed animation for these components.
- The block between Dan's animated object and Teresa's non moving section at the front should be moving. I animated this block and cloned it onto the other side of the central pump so both blocks moved the same way. Also, the blocks' rotation should reverse when they rotate by 90 degrees so I added this as well.
- Teresa's section at the front should be animated and both halves should move the same direction. I animated this front section.
Below is a video showing the completed animation loop. It contains the environment and textures, which will be discussed later:
As can be seen, there are no floating objects; the blocks rotate together and change direction once they have rotated 90 degrees; and Teresa's objects are animated.
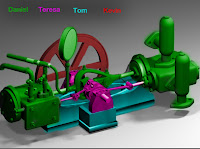
Upon receiving the first video of the animation loop from Kevin...
...It was good to see most of the animation in place. However, certain changes needed to made, which I did in class. The changes I made are:
- On the pump section in the centre, there are floating objects moving alongside Dan's main pump. These should be attached to the pole and not moving, so I removed the keyframed animation for these components.
- The block between Dan's animated object and Teresa's non moving section at the front should be moving. I animated this block and cloned it onto the other side of the central pump so both blocks moved the same way. Also, the blocks' rotation should reverse when they rotate by 90 degrees so I added this as well.
- Teresa's section at the front should be animated and both halves should move the same direction. I animated this front section.
Below is a video showing the completed animation loop. It contains the environment and textures, which will be discussed later:
As can be seen, there are no floating objects; the blocks rotate together and change direction once they have rotated 90 degrees; and Teresa's objects are animated.
Group Work- Combining and Alterations
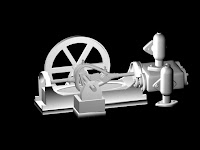
Above are the first images of everybody's contributions to the model put together with the exception of the exhaust, which Dan had yet to make. Putting the model together was achieved as a group effort in class and involved a lot of scaling and moving of models to fit the sections together.
As far as alterations to my chassis were concerned, I removed the awkward-looking top of my side sections and replaced them with supports made by Teresa. Also, the bottom half of my side section was extruded further to provide a more accurate shape with more depth.
After this image was rendered, the next step was to include Dan's exhaust and email the finished model to Kevin for animation.
Group Work- Modelling the Engine
Since the last meeting, it had become apparent that Dan could not model the entire engine alone and Teresa did not feel comfortable building the governor, so we divided the engine up into parts to model:
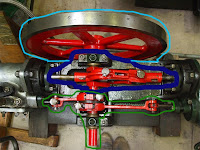
The wheel in light blue would be built by Kevin, the dark blue components in the centre and the exhaust/governor at either side would be built by Dan, and Teresa would build the components in green. My job would be to build the cradle the engine was placed in.
First, I required a reference plate image to work with. Luckily, Teresa had provided one as part of her additional research:
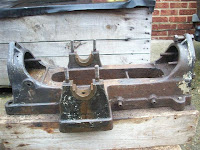
As can be seen, the chassis contains a lot of symmetry which made modelling easier. Below is my model in Max:
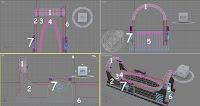
I will explain the model in sections:
1: "Loop at the top": The arch at the top of the model was a Torus which was converted into an Editable Poly. The bottom half was then removed and the remainder was scaled to fit.
2: "L shape section": This section was drawn using the Line tool and the main face was extruded to create a solid object. However, extruding the face led to a hole on one side of the model, so it was cloned and rotated to create a solid, filled L shape. This was then cloned 4 times around the model.
3: "Top section cover": This was created using the Line tool as well, and was extruded to give it depth so it extends to the bottom of the model. As can be seen, this was mirrored onto the other side of the chassis to create a bowl.
4: "Bowl": This Torus was added to the top of section 3 to smooth the edges out around the bowl.
5: "Back": This cube was added to the bowl section in the centre to provide a solid back and front section. As can be seen, it was cloned to opposite end of the model.
6: "Base": The base was a basic cube to provide a bottom to the model.
7: "Side supports": This section was mostly created using the Line tool and extruding faces to provide an approximation of the supports on the chassis seen in the photograph. Using the Line tool was a very complex way to do this and the sheer amount of cloning and rotating required told me I should have done this another way. The Torus in the centre is to smooth out the edge of the hole.
The screws around the model are cylinders placed in the correct position. The finished chassis with a very rough texture map looked like this:
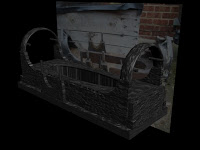
The next job was to join everybody's sections together into a coherent model.
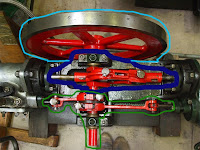
The wheel in light blue would be built by Kevin, the dark blue components in the centre and the exhaust/governor at either side would be built by Dan, and Teresa would build the components in green. My job would be to build the cradle the engine was placed in.
First, I required a reference plate image to work with. Luckily, Teresa had provided one as part of her additional research:
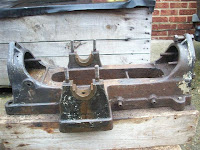
As can be seen, the chassis contains a lot of symmetry which made modelling easier. Below is my model in Max:
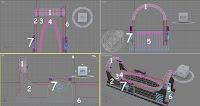
I will explain the model in sections:
1: "Loop at the top": The arch at the top of the model was a Torus which was converted into an Editable Poly. The bottom half was then removed and the remainder was scaled to fit.
2: "L shape section": This section was drawn using the Line tool and the main face was extruded to create a solid object. However, extruding the face led to a hole on one side of the model, so it was cloned and rotated to create a solid, filled L shape. This was then cloned 4 times around the model.
3: "Top section cover": This was created using the Line tool as well, and was extruded to give it depth so it extends to the bottom of the model. As can be seen, this was mirrored onto the other side of the chassis to create a bowl.
4: "Bowl": This Torus was added to the top of section 3 to smooth the edges out around the bowl.
5: "Back": This cube was added to the bowl section in the centre to provide a solid back and front section. As can be seen, it was cloned to opposite end of the model.
6: "Base": The base was a basic cube to provide a bottom to the model.
7: "Side supports": This section was mostly created using the Line tool and extruding faces to provide an approximation of the supports on the chassis seen in the photograph. Using the Line tool was a very complex way to do this and the sheer amount of cloning and rotating required told me I should have done this another way. The Torus in the centre is to smooth out the edge of the hole.
The screws around the model are cylinders placed in the correct position. The finished chassis with a very rough texture map looked like this:
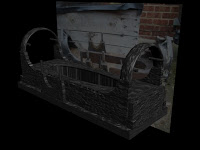
The next job was to join everybody's sections together into a coherent model.
Subscribe to:
Posts (Atom)